Formwork is an indispensable part of modern construction projects, being a temporary or permanent structure for holding poured concrete to take the shape of the mold. Before the hardness of the concrete, the formwork must have the desired shape and size. It must be oiled to allow the concrete to eventually strip off the other layer. Construction as a whole has also evolved to accommodate this technology, which is not new per se.

History has it that formwork has been around for as far back as the Roman civilization to accompany to use of cement. Also, the recent trend of events in construction companies and their projects suggests that computer-aided designs and structures are more vast, creative, and imaginative. These structures thereby require a unique approach to get things done at the best possible level of quality and effectiveness of production.
However, it also shows that many of these construction projects can be achieved faster, more effectively, and more safely. But none of these qualities are achievable without the appropriate structures in place, one of which is the suitable formwork. Moreover, the basic construction materials used these days can be far more robust and long-lasting than many that were in use several years ago. Therefore, it affords concrete builders and other categories of construction stakeholders to produce safer and more effective construction projects. If searching for property in Australia,look no further visit buyer agency
BKH Group Sydney Formwork Engineers
BKH Group has one of the most specialized formwork engineers who understand the dynamics of concrete structures. They also stay close to you to ensure that your building project meets the clearly stated requirements. More so, the main goal of the effectiveness of our site engineers is to ensure that we can optimize the quality of our delivery at the least possible budget cost and time. This intelligent solution to construction makes us value the opinion of our clients, and we even consider them more as partners to achieve the best quality of service delivery.
Customized Formwork Engineering Systems
BKH Group can provide a high level of concrete formwork quality for sophisticated construction projects that meet the exact needs of the project financier. Some of their essential services may cover the following:
- Civil engineering systems that cover construction projects such as bridges, underpasses, flyovers, shoring, and tunnels
- Horizontal systems that involve the use of formwork solutions that serve the purpose of slabs and shoring component structures
- Vertical systems for formwork solution that involves circular walls, walls, piers, and columns as required
- Props and shoring systems are the perfect option for shoring cut and cover tunnels with a good choice for high towers such as skyscrapers and high rise.
- Climbing systems are options for working on multilevel constructions using diverse platforms
Advantages of BKH Group in Formwork Sydney
There are some outstanding benefits to why you should choose the BKH Group for your concrete formwork projects. For instance, we provide a state-of-the-art solution to customers’ demands. We ensure that there are no delays in the project delivery. At the same time, we also consider the specific weather conditions of Australia as a country. In addition, we factor other technical issues peculiar to the Sydney marketplace and provide innovative innovations that set us above others. Below are some exciting advantages that we have above our competitors;
- We have a widely accessible area that is specifically dedicated to an assemblage of formwork systems, depending on the project at hand
- As we execute the manufacturing process of formwork under a closed environment, we ensure that natural conditions do not affect project delivery and not at this stage. Meanwhile, our assemblage of formwork component structures is appropriate for ensuring we make our delivery in due time. This method also applies to prefabricated formworks.
- We ensure our fabricated tables serve ergonomic purposes through adequate working heights that remain safe for all our working team, especially those in the assembly sector
- All fabricated designs are essentially cost-effective and suitable for freighting to the site as soon as they are done
- Besides, we can also use forklifts to move the panels and products out of the warehouse to the required nearer destinations
- Finally, our clients have access to our team of technical experts who can provide professional services
Cost of Formwork
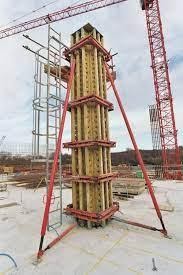
Concrete formwork is inarguably a widely used structure that can manage the costs and quality of final delivery. As a result, one of the factors to consider in projecting a project budget cost is the actual cost of using formworks. When you decide on the appropriate formwork to use and the construction plan aspects that require formwork, it becomes easier to make accurate projections.
Suppose one requires a formwork for a horizontal surface. In that case, that is relatively cheap to use because you only need supporting stakes to bare plywood. However, when you need to erect formworks for staircases, walls, second-story floors, and columns, those structures are more expensive than the simple horizontal formworks. The primary reason for the increased cost is that they require much more materials, more accurate specifications, and a more detailed approach. Remember that time is also one of the prices to pay when considering the capacities of the final project.
Some of the components that determine the cost of formwork generally include the cost of materials, supplies, and the labor that will do the physical work. Therefore, this item varies by the project size, the season of the project, and at times, the required duration to get the job done. The articles are also replaceable, depending on some of these factors and other related ones. For instance, a simple job of creating a driveway or patio may only require one laborer. More complex jobs will need an experienced operator of large machines and specialist supervisors to be on the ground.
Below is a typical breakdown of the cost of financing a project with the formwork section only.
Item | Total ($) |
Formwork costs | 100 |
Labour costs at the rate $40 per hour (6 hours per day) | 240 |
Formwork Job Supplies | 40 |
Formwork Equipment allowance | 50 |
Total | 430 |